Cloud Cities Barcelona
TOMÁS SARACENO
Faced with such a technical challenge, it was liberating to be encouraged to develop and explore different solutions.
We pushed material to its limit to ensure it would be safe for public interaction. Materials were subjected to extensive internal stress testing by our design engineers, and were independently verified by an external company. Due to European law, we allocated time into the project for additional tests to be conducted in Spain to gain additional certification, confirming that the installation was safe.
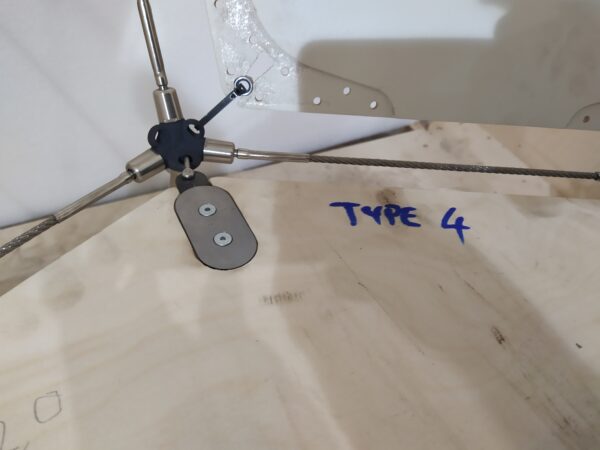
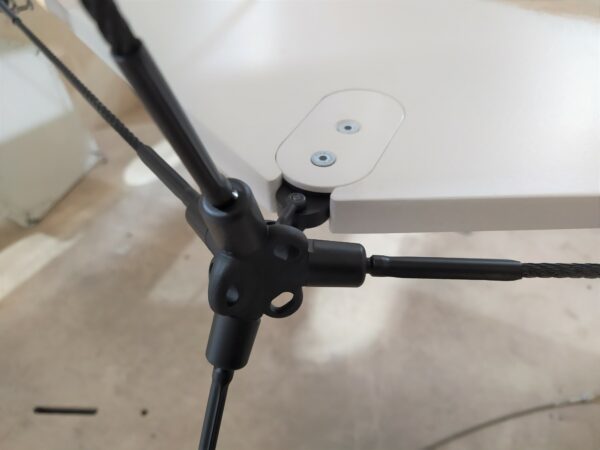
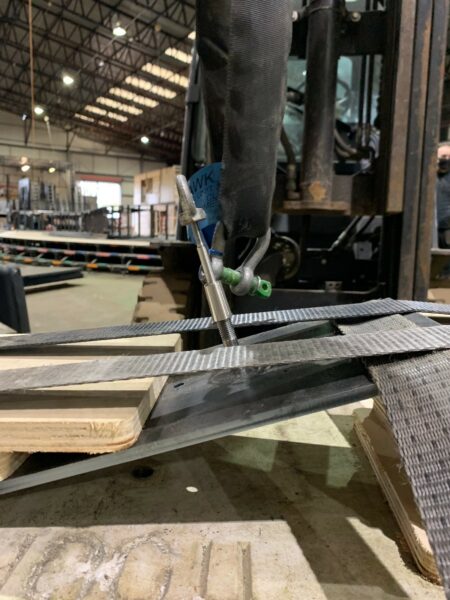
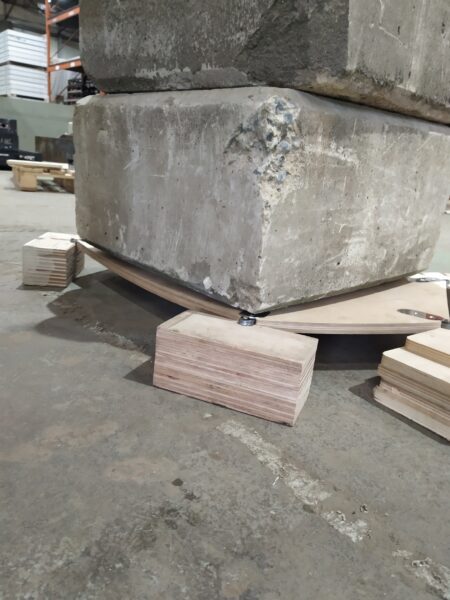
The consultancy period allowed the team to design, prototype and test about 25 variations of custom-made nodes and cable connections, panels, anchors etc. In the end, there were six variations of inner net nodes, all cast from stainless steel. The 230 outer nodes were made from super high-strength steel plate – each one unique.
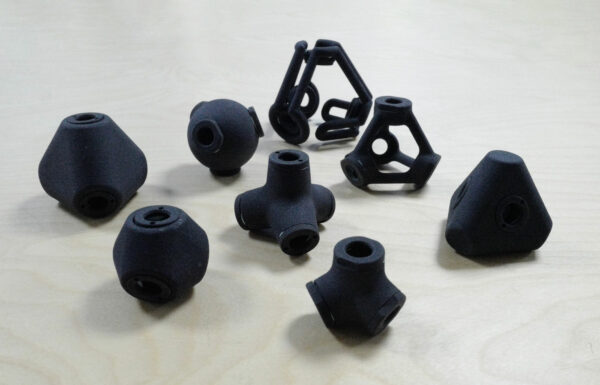
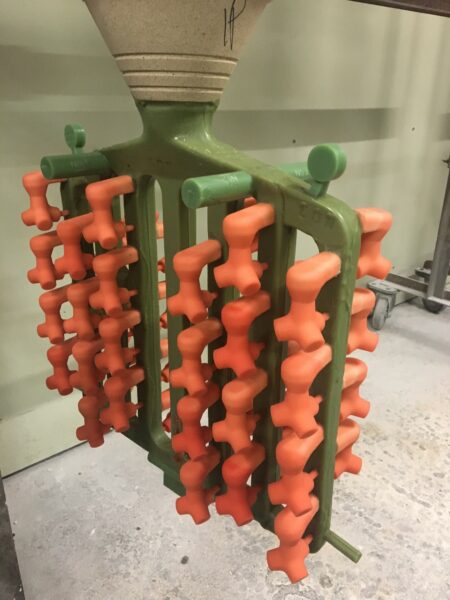
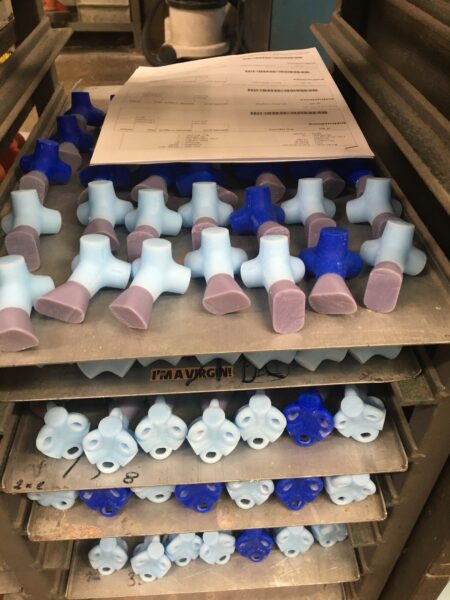
The fins of each anchor needed to be symmetrically aligned to the cable vectors – it was imperative to get this right. However, we were in a difficult situation as we couldn’t design the anchor cables until we knew where the anchors were, and we couldn’t design the anchors because we didn’t know the angle of the cables.
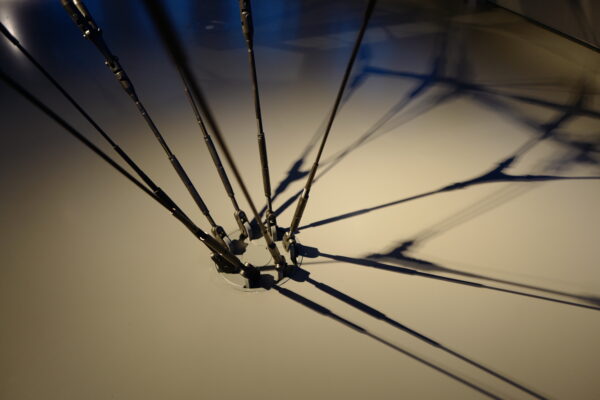
A test build was conducted at our facility on the outskirts of York.
We invited the creative team to interact with their design. We were then granted sign off to proceed with the full-scale build.
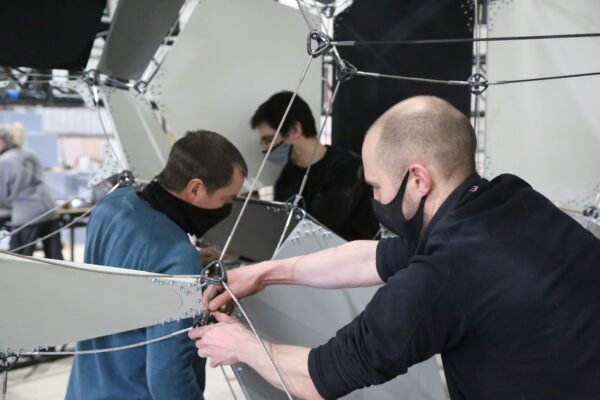
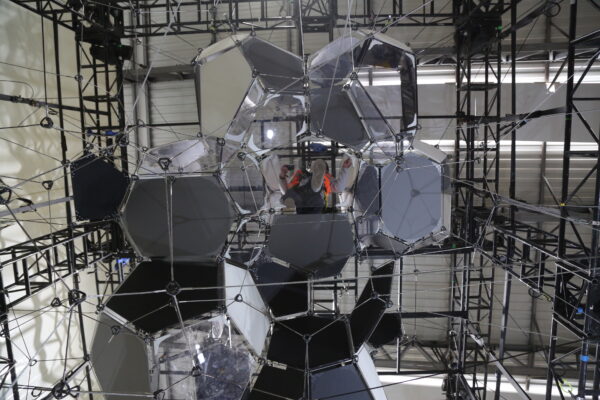
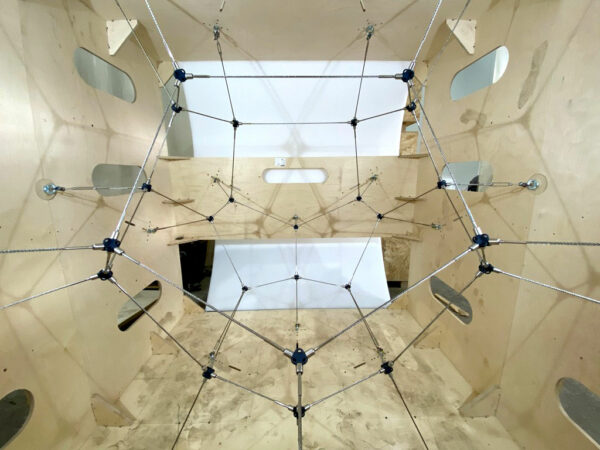
The full-scale build and installation
The relatively simple outer net was hung first, using a team of local riggers, followed by the inner next ‘strings’. Due to the complex layering, we were unable to use scaffolding because it would interfere with lower levels of the sculpture. Therefore, we had a pair of access nets made. These were strung across the space and tensioned to provide a stable platform. Once a layer of strings had been completed, the netting was dropped down to the next level, and so on, until the sculpture was complete.
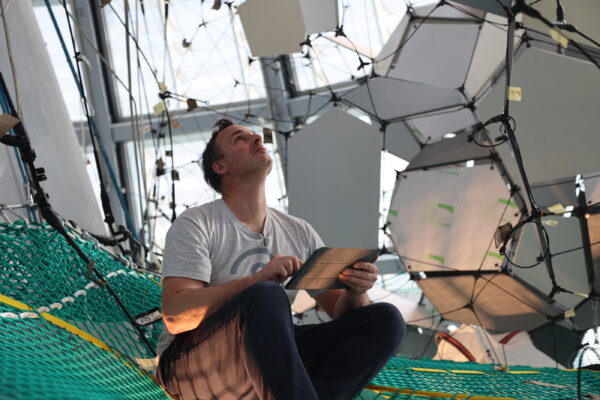
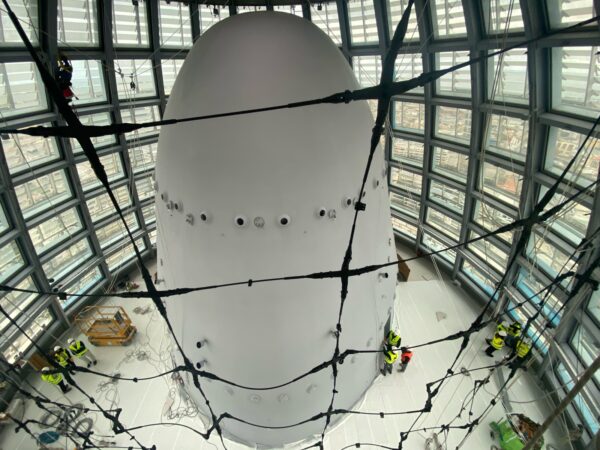
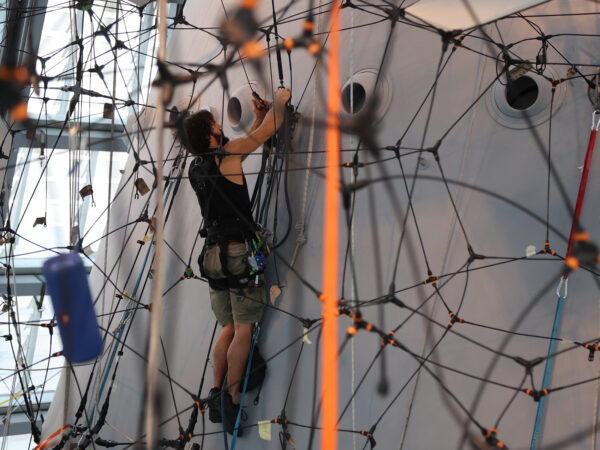
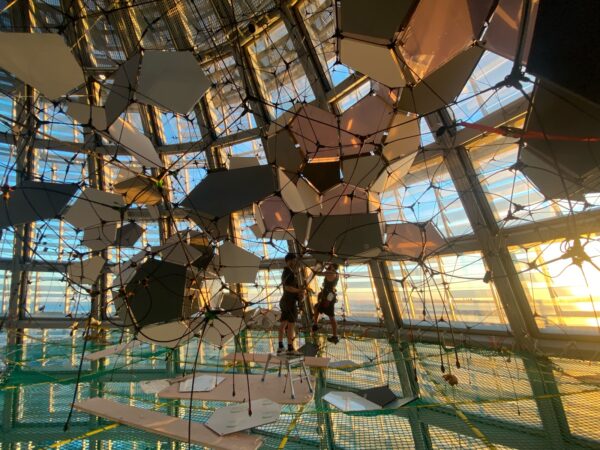
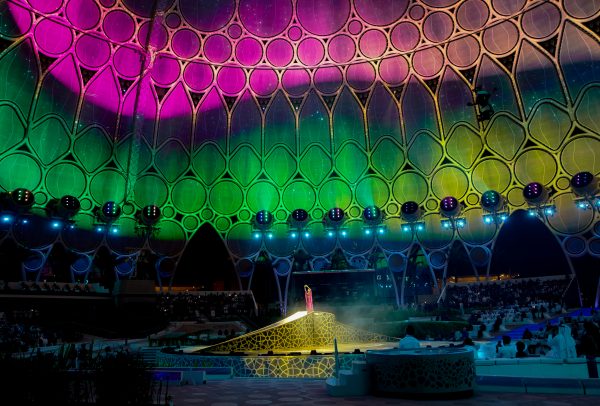