London 2012 Olympic Games
DANNY BOYLE / THOMAS HEATHERWICK
The Cauldron aka ‘Betty’
6.5m diameter
204 petals
Tapered steel stems (up to 9m long)
3mm copper sheeting hand beaten into shape
9 months of development
The journey from model to reality began with Andrew Taylor’s 3D Rhino model which was exported as solid geometry to be used in our Autodesk Inventor software. This gave us the freedom to experiment: swapping materials with their different weights and strengths, to refine the model and to produce detailed instructions for the CNC machines. Our in-house CAD team modelled the cauldron’s components, as well as the gas and electric feeds. Each stem was attached to a system of six components that formed the pivot, which in turn was attached to the tiered cauldron base. Originally much bulkier, the refinement process allowed us to reduce production time from 5 hours to 50 minutes. The cauldron petals were the perfect synthesis of the artistic and the technical. Each one had to interlock with its neighbours so that when closed, the petals formed the tight-fit bowl shape required. The array of stems was so tight, that just 1º of error would have resulted in a meshing of adjacent petals. Each of the 204 unique hand-wrought 3mm copper petals enfolded a gas lit flame, the rim of each petal etched with the name of a participating nation. Three complete sets of petals were made, and it took six hours to hand beat the 3mm copper sheet into the delicate shape required for each one. Three sets were made: a rehearsal set, Olympic set and Paralympic set: a total of over 600 petals.
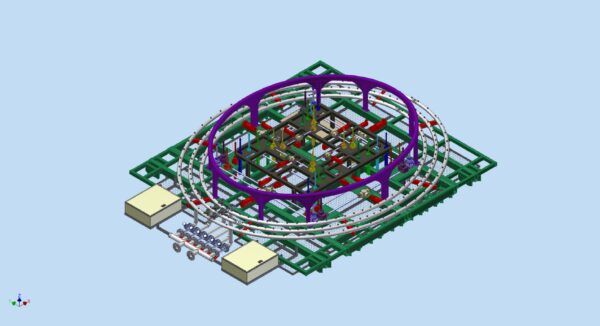
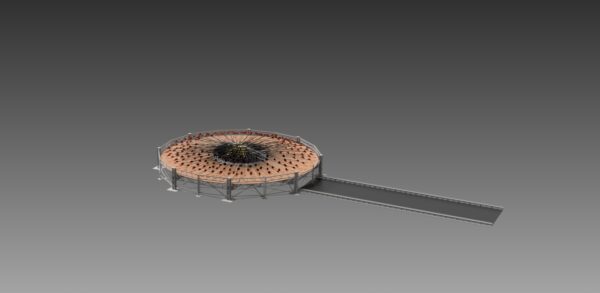
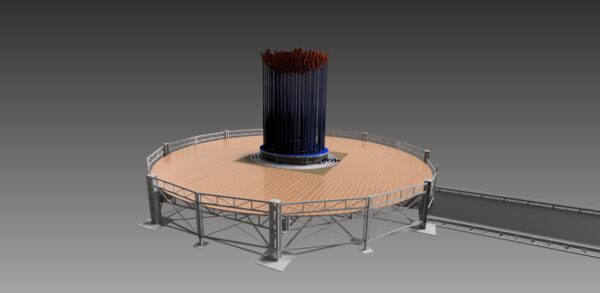
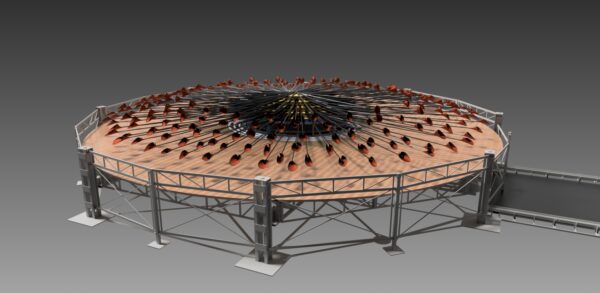
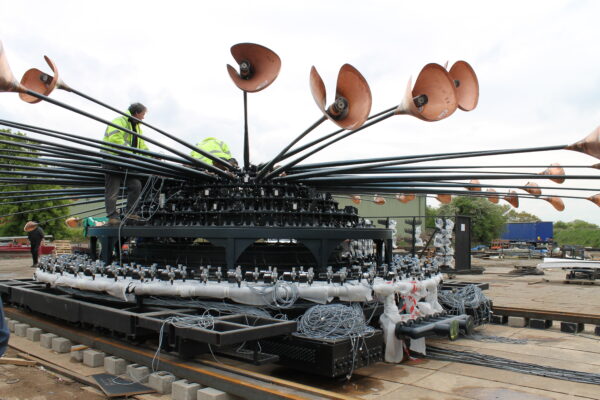
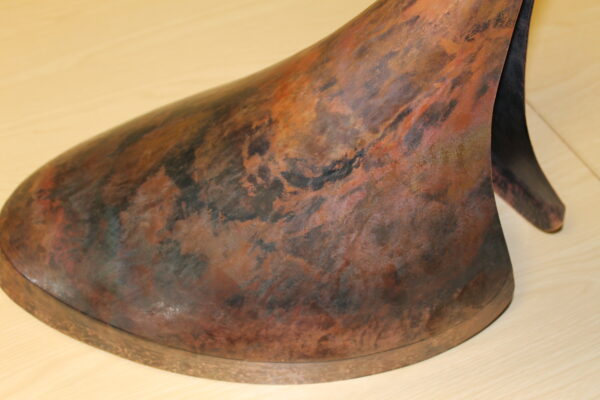
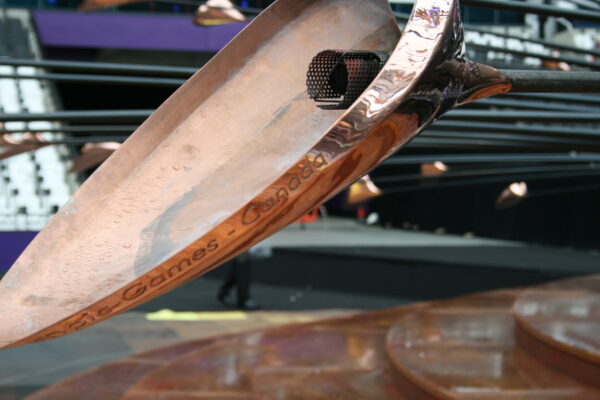
A Powerful Reveal
In order to move Betty from her concealed position under the stage, we needed stage engineering capable of lifting all 16 tonnes of her to the stage surface. At 18m diameter and weighing 32 tonnes, stage lift ‘Frank’ was the largest lift we have ever built. ‘Frank’ was positioned snuggly within the frame of the 18.5m wide stage aperture, a total of eight rams supplying the power via eight lift towers to raise Betty the two metres to show position.
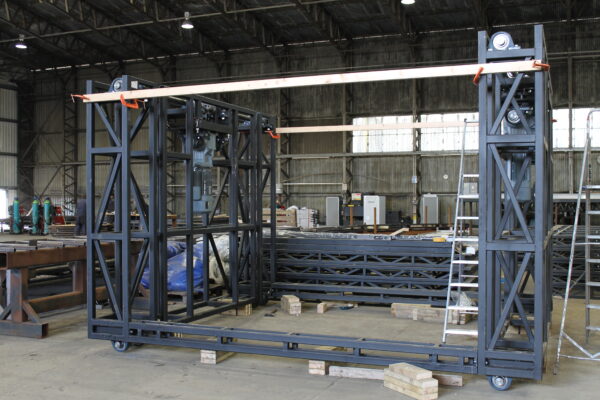
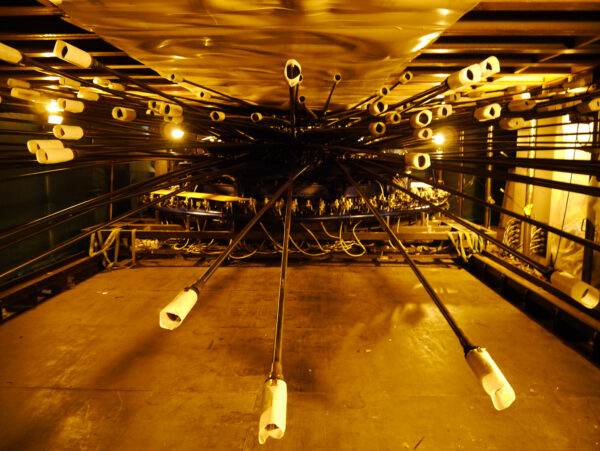
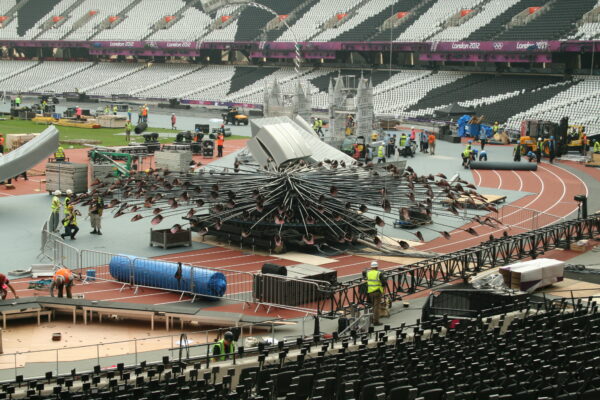
The Ceremony
Engineering the Industrial Revolution
The cable net and our Qmotion automation system was used to fly performers and scenery for key dramatic moments in the ceremony. The transition from ‘Green and Pleasant Land’ to the ‘Pandemonium’ segment was quite possibly the biggest scene change in history. One constant throughout the ceremony was the huge 10 metre waterwheel which survived the transition from the opening pastoral scene through the industrial revolution of Pandemonium when further scenic elements were added – namely the five 10m by 3m beam engines. Manufactured in 3800mm sections, the 8m diameter wheel of each beam engine had to be light enough to be carried on by the performers and simple enough to fit together on stage amid the noise and live action of the show. Constructed in our workshops they were made from fully recyclable lightweight aluminium frames clad with plywood and given a suitable basic paint finish, before being finished in detail on site by others, giving the appearance of heavy iron and steel. Each device rotated or nodded via concealed chain drives. Following fabrication, the waterwheel was given a distressed scenic finish, making it look as if it was made from weathered oak and cast iron – complete with touches of verdigris. Although real water passed through the race beneath, the wheel was driven mechanically.
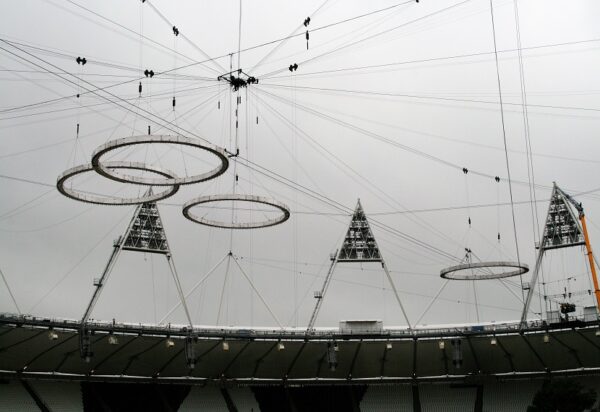
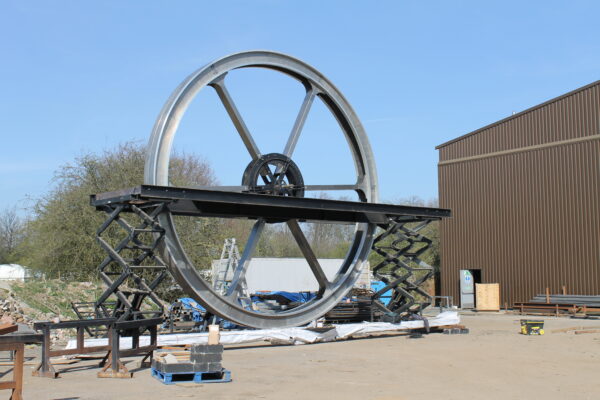

QMOTION
Qmotion played a vital role in delivering the slowly building crescendo of seamless scenic changes. Our systems in the air and under the stage raised the seven giant chimneys, the tallest of which reached a height of 30m. Although inflatable, each double-skinned chimney still weighed around one tonne and was rolled via tracks underneath the stage onto one of our stage lifts. As the chimneys were simultaneously inflated by fans and pulled skywards by our cablenet system, the stage lift rose, finishing flush with the stage floor as each chimney reached its full height. Convincingly rigid and solid in appearance, steeplejack performers then ‘scaled’ the chimney heights.
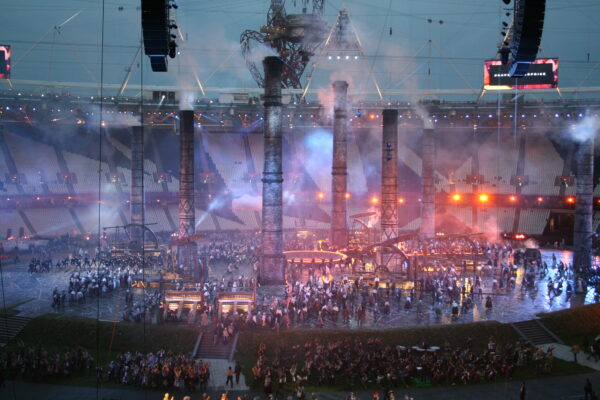
Forged Olympic Rings
Qmotion controlled the four huge 15m diameter ‘molten steel’ rings that flew from platforms on the roof, as the fifth freshly ‘forged’ ring was lifted from the centre of the stadium. These five rings reconfigured in mid-air above centre stage, perfectly choreographed into the iconic Olympic symbol. Which occurred simultaneously with the raising of the chimneys. This section required careful planning and timing as up to 3.5m of deflection in the aerial cables had to be allowed for due to the changing loads on the aerial system. This process then had to be reversed as the stage area was cleared for the NHS segment of the show.
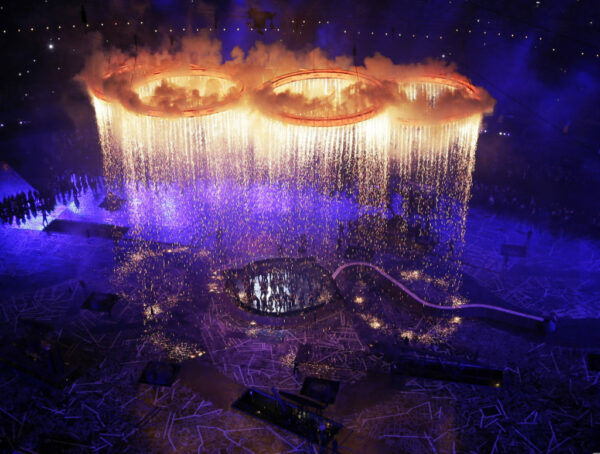
Flying in 32 Mary Poppinses required four flying lines, each loaded with eight performers. Descending from platforms on the roof, the Mary Poppins performers flew down into battle with a huge Voldemort puppet, which was also controlled with lines to our aerial system. At the same time, five performers dressed as Dementors took off from the stadium stage floor. All required careful coordination and programming to ensure each performer was kept to within their own ‘airspace’ and the correct speed of travel was maintained.
The aerial system was used for further elements of the show such as deploying the top half of the house that lifted to reveal British inventor Sir Tim Berners Lee and later, in a unique take on the traditional doves of peace, we launched the lone cycling ‘dove’ performer into the air.
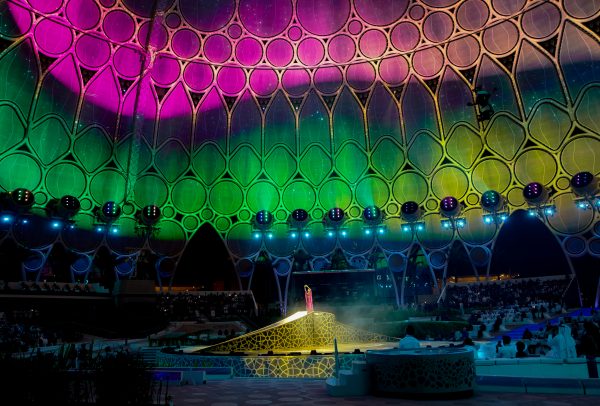