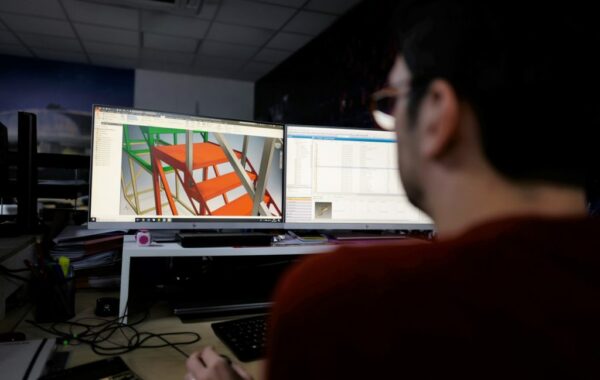
As part of Amazon Fashion – Destination Denim, we were to supply a tread unit with a total rise of 3 metres, but that could be broken down for storage and quickly re-assembled without the use of lifting equipment. No section of the tread unit was to weigh more than 80kg, with no lifts over chest height. In addition, we specified a 1500kg load (one person per step) with a high safety factor, with high stiffness and low deflection to ensure the tread unit felt solid and secure.
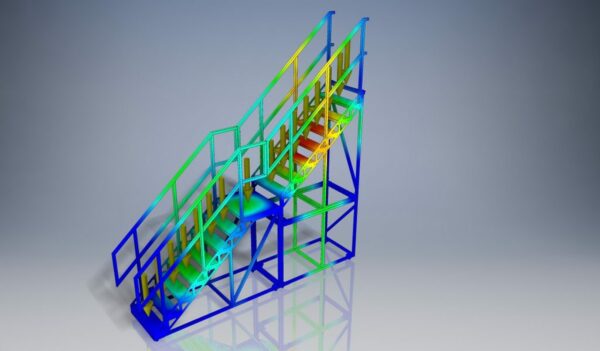
Typically a steel staircase comprises steel box-section framework for both treads and risers, with steel plate treads and risers. Our methodology replaced this complex framework with laser-cut steel stringers and lightweight tread beams, assembled with welded slot-and-tab connections.
This saved weight, reduced material usage and cutting time, and also provided a self-jigging assembly requiring fewer welding operations.
Open risers and phenolic ply treads provided additional weight saving. The use of FEA software provided guidance for further weight reduction. By analysing stresses and deflections in the tread unit assembly, we were able to identify areas in which material could be reduced without compromising the design intent.
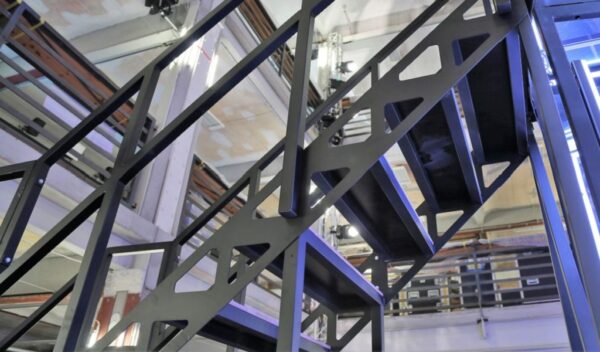
Most notably, by incorporating a handful of small reinforcing gussets into the framework design, we were able to halve the thickness of the steel stringers. We identified that we could reduce the number of cross-braces by combining the stringers into the cross-bracing design. In addition, through some on-screen experimentation, we found that increasing the depth of the stringers whilst adding cut-outs both increased stiffness and decreased weight.
The finished tread unit has very low deflection (0.25mm on the treads, 3mm on the handrail), and a maximum section weight of 80kg, some 40% lighter than the first iteration. A focus on CAD development resulted in decreased material use, lighter weight, faster fabrication, and easier installation.