Stage One Stories with Lewis Earl
Interview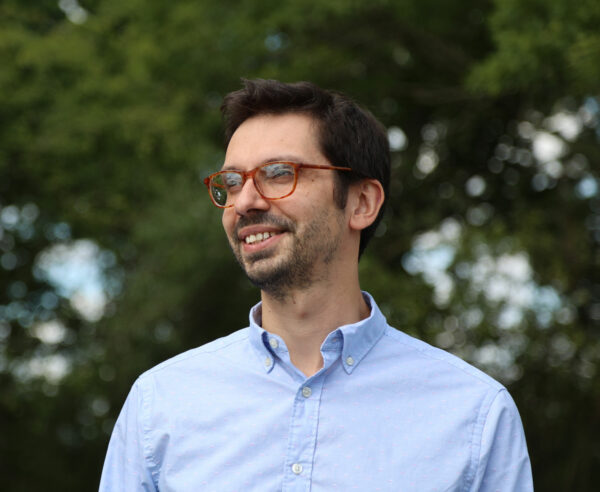
Lewis Earl, Consultant Design Engineer, could be considered one of the lynchpins in project delivery at Stage One. Lewis provides guidance for internal and external engineers, designers, and clients to progress ideas into practical design methodologies. Lewis is a key member of our consultancy team. He leads on research and development and inputs on tenders and design reports. As part of his role, Lewis also develops prototypes and tests potential solutions, and provides feasibility studies that inform the production process.
Lewis has been the lead designer on some of our recent high-profile projects including the Ed Sheeran Mathematics tour, and Cloud Cities Barcelona. Having started his career at Stage One as a composites fabricator, Lewis has returned to his roots following a degree in product design and a stint designing, and installing theme parks and visitor attractions in the Middle East. In this Stage One Stories, Lewis shares his highlights, discusses his design approach, and explores how the industry could develop…
What keeps your spark alive for Stage One?
Variety. I enjoy problem-solving, and Stage One certainly gets approached with some unusual engineering problems. I’m fortunate to be involved as soon as client concepts land. Developing design methodologies so early in the process also gives me a lot of creative freedom, which I really value. I get to work closely with our account handlers, engineers, designers, and fabricators. I have contact with every single part of the company, so I get to understand the constraints that each department faces and can develop solutions that satisfy everyone. Finally, we have some amazing clients – developing a good relationship with them, and seeing their reactions when beautiful concepts are brought to reality, is very satisfying.
How do you approach a new design?
Every project has its own challenges, so I try to answer the big questions first – or, at least I try to figure out what the big questions are. Size, shape, schedule, budget, location… Then I identify technical hurdles and see how they could affect the build. When I’ve looked at the design from different angles, my next step is to split the project into mini projects, each with its own scope and specification, and check that they will work together.
All of this is done collaboratively, with input from our own engineers, project managers, and fabricators. Big inter-departmental kick-off meetings allow us to bounce ideas around quickly and keep projects moving, but it’s vital for design engineers to spend time on the shop floor talking to fabricators. They’re the experts, so it’s beneficial to understand the intricacies of their field and I try to tailor designs to their strengths.
Once we’ve developed a firm specification and one (or more) potential solutions, we present these to the client. There’s usually a lot of discussion, development, and a few iterations. Often, we are awarded the full build contract; other times, we act as consultants.
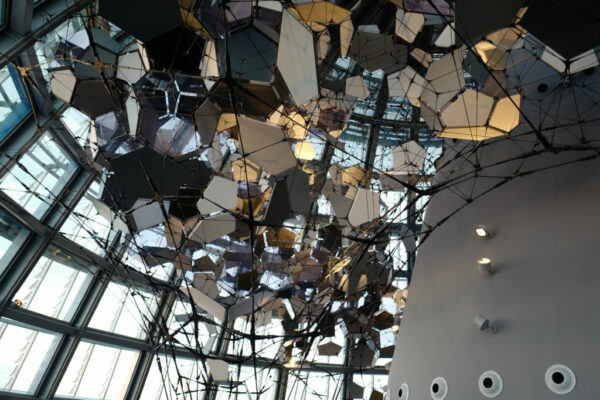
If you had to pick one, what would your favourite project be?
Definitely Cloud Cities in Barcelona. Our client had a stunning vision — an enormous climbable cable sculpture, suspended within the glass-domed top of the 130m Mirador Torre Glòries, providing a 360˚ cityscape in the centre of Barcelona. However, other than the artist’s vision, the only constraints we had were the maximum tensions allowed in the cables — the connecting parts, the panels, the anchors etc only existed in the artist’s mind. This meant that almost every single piece of hardware, literally down to the nuts and bolts, was designed by us to meet very tight technical performance specifications, whilst also satisfying the artist’s even-tighter aesthetics. There were 9,000 cables, most of which were unique in terms of length and hardware; 6,000 beautiful cast steel nodes, which were the result of 20 rounds of prototyping and mechanical testing; 230 unique cruciform nodes made from ultra-high strength steel, for which we wrote a plugin for our design software just to generate the geometry… and we built a room-sized jig to start the pre-assembly before the months-long on-site build in Barcelona. I’ve never worked on a project with so many complex engineering and aesthetic challenges, but at the same time with so much technical freedom. And working in Barcelona for a few months was nice, too. We’ve had some great feedback from the team at Mirador Torre Glòries; they’re welcoming approximately 200 guests per day.
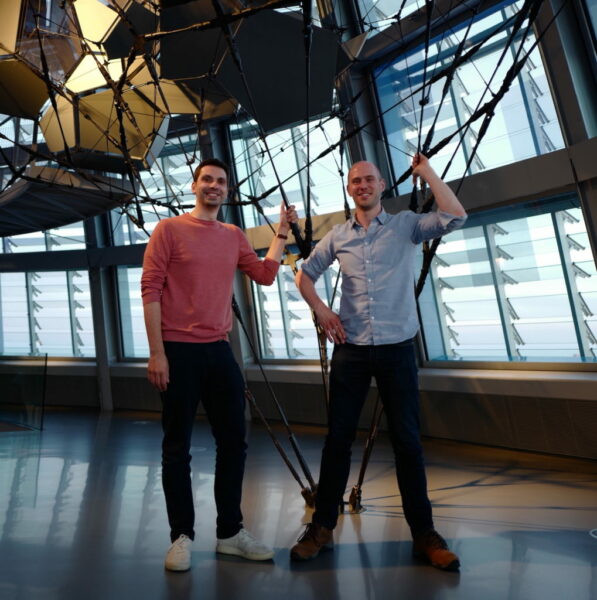
How do you think the industry is developing?
This is tricky, as Stage One aims to be a leader of creative engineering; quite niche in a very broad industry. However, within our own sphere, it sometimes feels like a split is emerging. On one side, this country has a pool of talented engineers who, using traditional methods, can make an accurate structure using hammers and pieces of string. It’s a skill, but one that can easily stagnate or be lost if companies don’t invest. On the other hand we see a lot of complex and beautiful concepts, designed by talented young designers and engineers using clever cutting-edge software – but without too much thought as to how it could actually be built. If the two sides had more crossover, it would be beneficial for both.
I wonder what the engineering industry will look like in 10-15 years when a large cohort of traditional fabricators will have retired. I hope that engineering fabrication companies invest in apprentices, machinery, and software so that traditional skills are built upon rather than lost, and that concept designers can spend a bit of time on the shop floor so their ideas are grounded in reality.
I think Stage One is bridging this gap very well, both in terms of people, and machinery and software investment. We have people who are dedicated to their discipline with decades of experience, and we’re also taking on fresh talent. Our production team has recently launched apprenticeships and training programmes, so we’re building and securing the future of design and manufacturing in-house.
Do you have concerns about the future of the industry?
Again, it’s quite hard to answer as engineering covers such a broad scope. Sustainability is obviously a big one. It’s difficult because in some ways engineering is the solution, in others, it’s the cause. I don’t think any industry is moving fast enough. But things are changing – we’re introducing materials and methods that we wouldn’t have considered 20 or even 10 years ago. Recycled and recyclable materials are being used more in construction and manufacturing, and we’re educating ourselves on best practice and passing that knowledge and recommendations onto clients. We’re recycling more steel and other metals within our projects, and our MD, Tim Leigh, is a conference panellist on using steel sustainably. We recently installed some video plinths for About Us, a touring event and part of Unboxed 2022, which were predominantly clad in a 100% recycled plastic product. We also recently built and installed part of the ABBA arena in Stratford – a few years ago we might’ve made this from steel, but with some R&D we were able to produce this from glulam timber instead. Now we can recommend this to new clients – in fact, the Sky Retail Pods installation used the same technology.
We’re doing research and development to explore alternative resources and, as more clients are demand sustainable solutions, we’re supporting that effort. It’s going to be a massive challenge for us, and for the industry, but that’s part of the fun. And it’s another skill we can learn as a company, which will support and secure Stage One’s place within the industry.
What do you hope the future holds for Stage One?
We’re investing in smart people and new high-end software and machinery, which means that we can bid for larger and more complex jobs across the world. Personally, I would like to see more permanent installs, like Cloud Cities, as they can be made more sustainable. And from my point of view, I relish the complexity of projects, so that would certainly be on my wish list for the future.
If you have an engineering project that you would like to speak to Lewis and the team about, please email enquiries@stageone.co.uk and a member of the team will be in touch.
Cloud Cities Barcelona was designed by Tomás Saraceno and is in residence at Mirador Torre Glòries. More information on experiencing the sculpture, along with price details can be found on the Mirador Torre Glòries website (please note this link will take you to an external website).