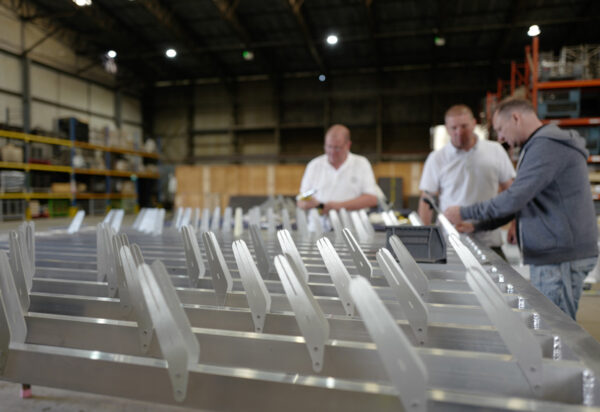
We inhabit two worlds. Fabrication and construction. One informs the other and there is a reassuring sense of linkage between the processes of making and building.
From a programme perspective, this relationship isn’t symmetric. In our world, we almost always have longer to design and fabricate than we do to construct. This is largely due to restrictions on site access, the prohibitive cost of venue hire or the fact that there is a preceding show or installation ahead of us.
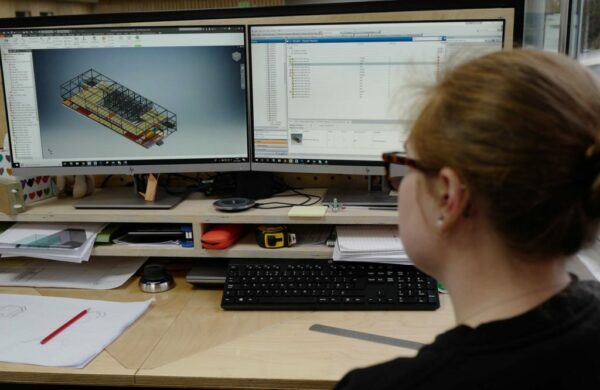
It’s a persistent challenge and as a consequence one we’ve become quite good at solving. We start with end in mind. As an example, we knew that the BBC Pavilion at MIPCOM was to be erected on site in just six days. That gave us just twelve shifts of twelve hours to build a two-storey pavilion with a footprint of 35m x 15m. This could only be achieved by factoring this short install window as a constraint into the design process.
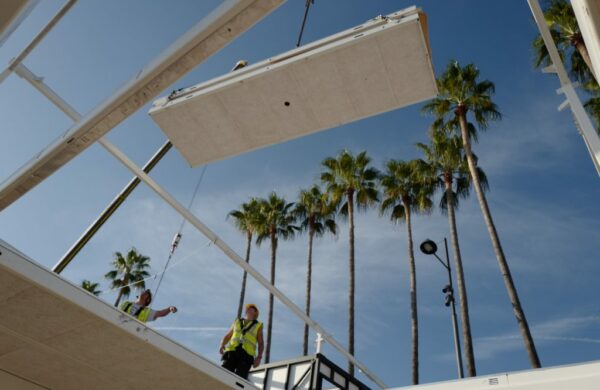
And so whilst having longer install periods is something that we often dream of, constrained installation will often inform design in the same way as gravity, weight loading and material prices.
Our experience is that being clear about the minimum available install window from the outset is critical. Wishing for more time rarely works and hoping beyond hope that the installation will all go without a hitch generally doesn’t work either. So embrace it. Think hard about design, insist on a test build to iron out the unexpected, and let Old Father Time have a seat at the table during each design crit.
So where’s the evidence that this works? If we return to the BBC Pavilion, just how did time constraints inform the design of the structure?
- The base frame detail provided accurate levels quickly upon an uneven venue surface.
- Structural steel members each had locating bosses and wedged receiving plate details to allow for fast and accurate dropping into position.
- Modular floor cassettes were designed to be rapidly craned into position.
- Design of prebuilt core meeting room units that could be lifted directly from a truck onto the structure.
- A series of facade units that were hung from the external members rather than face fixed.
- Rapid deployment tensile roofing that was pulled over the entire structure providing a quick and effective rain screen.
So did everything go swimmingly on site? Of course not. As with all projects there were some unexpected bumps in the road. It wasn’t easy. But it did open on time. Just one hundred and forty-four hours from unloading the first truck.
And it looked nothing like a temporary structure. Certainly nothing like a structure that had been built in twelve shifts. On this basis, although he’s the most expensive design engineer we’ve got, we’ll keep inviting Old Father Time to all of our design reviews.